
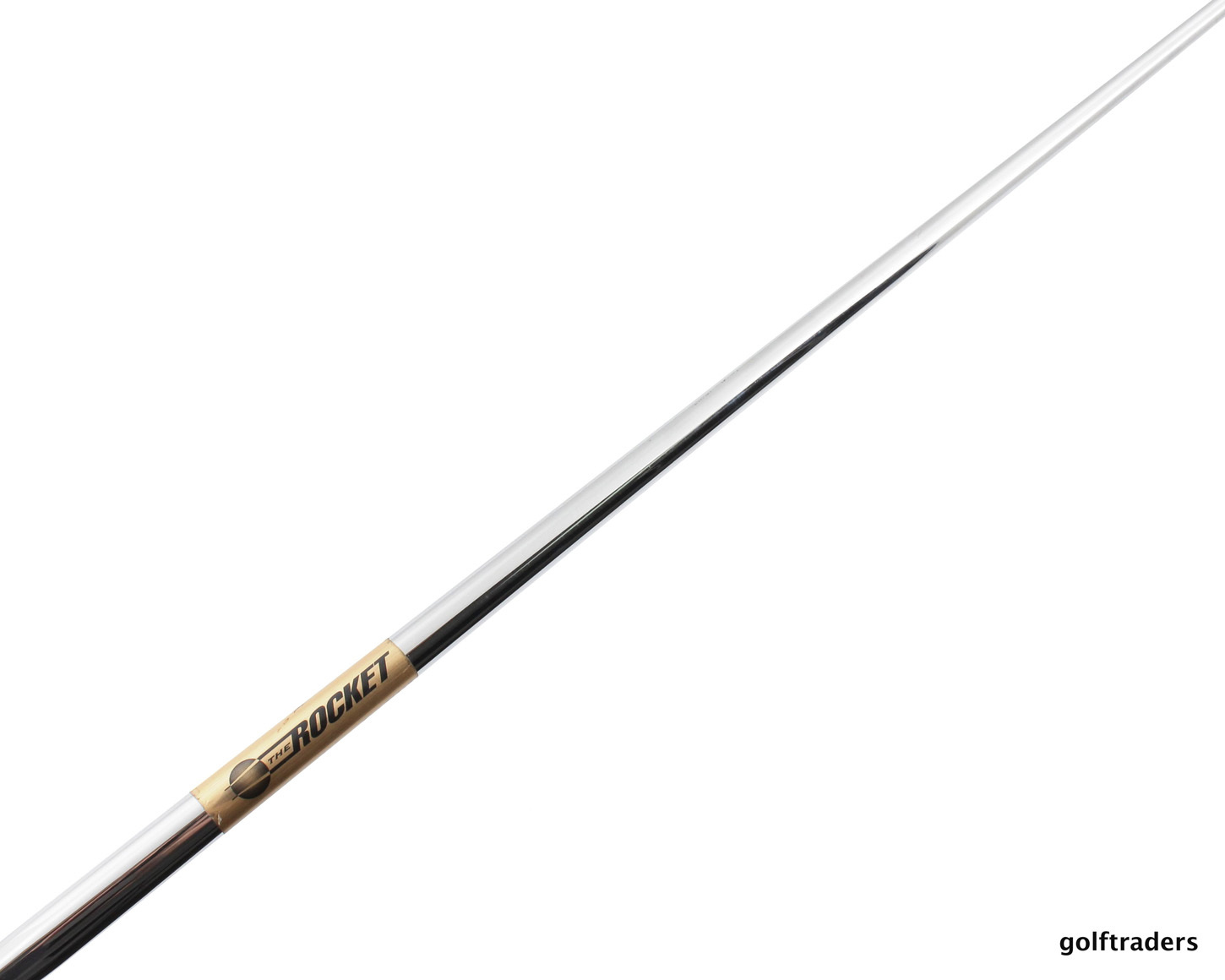
Subsequent aging ( precipitation hardening) of the more common alloys for approximately 3 hours at a temperature of 480 to 500 ☌ (900 to 930 ☏) produces a fine dispersion of Ni 3(X,Y) intermetallic phases along dislocations left by martensitic transformation, where X and Y are solute elements added for such precipitation. This is followed by air cooling or quenching to room temperature to form a soft, heavily dislocated iron-nickel lath (untwinned) martensite. The steel is first annealed at approximately 820 ☌ (1,510 ☏) for 15–30 minutes for thin sections and for 1 hour per 25 mm (1 in) thickness for heavy sections, to ensure formation of a fully austenitized structure. There has been Russian and Japanese research in Fe-Ni-Mn maraging alloys. There is also a family of cobalt-free maraging steels which are cheaper but not quite as strong one example is Fe-18.9Ni-4.1Mo-1.9Ti.

That family is known as the 18Ni maraging steels, from its nickel percentage. The higher grades have more cobalt and titanium in the alloy the compositions below are taken from table 1 of MIL-S-46850D: Maraging steels are usually described by a number (e.g., SAE steel grades 200, 250, 300 or 350), which indicates the approximate nominal tensile strength in thousands of pounds per square inch (ksi) the compositions and required properties are defined in US military standard MIL-S-46850D. Corrosion-resistance can be increased by cadmium plating or phosphating. Non-stainless varieties of maraging steel are moderately corrosion-resistant and resist stress corrosion and hydrogen embrittlement. The steels can be nitrided to increase case hardness and polished to a fine surface finish. Since ductile FeNi martensites are formed upon cooling, cracks are non-existent or negligible. Due to the high alloy content maraging steels have a high hardenability. When heat-treated the alloy has very little dimensional change, so it is often machined to its final dimensions. Maraging steels offer good weldability, but must be aged afterward to restore the original properties to the heat affected zone. Prior to aging, they may also be cold rolled to as much as 90% without cracking. Properties ĭue to the low carbon content (less than 0.03%) maraging steels have good machinability. The latter effect enables the design of maraging-TRIP steels where TRIP stands for Transformation-Induced-Plasticity. Hence, depending on their manganese content, Fe-Mn maraging steels can be fully martensitic after quenching them from the high temperature austenite phase or they can contain retained austenite. The manganese has a similar effect as nickel, i.e.
ROCKET GOLF SHAFTS STEEL PLUS
Alternative variants of nickel-reduced maraging steels are based on alloys of iron and manganese plus minor additions of aluminium, nickel and titanium where compositions between Fe-9wt% Mn to Fe-15wt% Mn have been used. This also indirectly increases hardenability as they require less nickel high-chromium, high-nickel steels are generally austenitic and unable to transform to martensite when heat treated, while lower-nickel steels can transform to martensite. Addition of chromium produces stainless grades resistant to corrosion. The common, non-stainless grades contain 17–19 wt% nickel, 8–12 wt% cobalt, 3–5 wt% molybdenum and 0.2–1.6 wt% titanium. Original development (by Bieber of Inco in the late 1950s) was carried out on 20 and 25 wt% Ni steels to which small additions of aluminium, titanium, and niobium were made a rise in the price of cobalt in the late 1970s led to the development of cobalt-free maraging steels. Secondary alloying elements, which include cobalt, molybdenum and titanium, are added to produce intermetallic precipitates. The principal alloying element is 15 to 25 wt% nickel. These steels are a special class of very-low- carbon ultra-high-strength steels that derive their strength not from carbon, but from precipitation of intermetallic compounds. Aging refers to the extended heat-treatment process. Maraging steels (a portmanteau of " martensitic" and "aging") are steels that are known for possessing superior strength and toughness without losing ductility. Steel known for strength and toughness Steels
